Welded Brackets for Floats in a Seaplane
Technical Report – Welded Brackets for Floats in a Seaplane
Instructions:-
Select one option from the list below:
1) Welded bracket for the floats on a sea plane.
2)Emergency door release handle from outside the aircraft on a medium sized airliner.
3)The frame underneath a passenger seat that is bolted to the rail on the floor.
Write this report as if you are the company’s material expert and the design manager has asked for your input and a report to present to the designers. If you make any assumptions, you must highlight those assumptions.
What are the material requirements for the component you selected? You need to state the basic alloy and if any additional or exact requirements are demanded. During the manufacturing process, are there any inherent material weaknesses introduced that must be addressed? What limitations in design or application might need to be stated?
You are required to use the Technical Report Template.
(Provided above)
The main body must not exceed five pages.
All references must be cited using current APA format.
This assignment will be submitted via Turnitin, a plagiarism detection tool
Solution
Welded Brackets for Floats in a Seaplane
Technical Report – Welded Brackets for Floats in a Seaplane
Executive Summary
A seaplane is an aircraft that is specifically designed to land or take off on the water. The control and operation of these planes happen in almost a similar manner as in a landplane. However, seaplanes are subjected to inherently challenging environments and thus are specially fitted with components that help maintain its stability, make it buoyant, and reduce its drag as well as preventing the plane from flipping or tipping as it moves through the water. With most of the world waters being slat laden seas and oceans, the planes are also exposed to effects of corrosion. Thus, the material that makes these components should have the right characteristics to ensure the safety of the plane and prevent extreme devaluation.
Introduction
Floats are a part of the plane’s landing gear. Flying boats, as these planes are commonly referred to can optionally be equipped with either a single float or twin floats. Most seaplanes are usually fitted with two floats. Floats increase a plane’s empty weight while decreasing its useful load and subsequently its rate of climb. Floats are attached to the rest of the plane through brackets which are either securing them mechanically or are welded to a float’s surface. Through movement in the water, the float’s brackets are subjected to extreme conditions including salty waters, strong wave action and further face the risk of damage in various plane operations. Consequently, this component must be made up of material that can withstand these conditions to guarantee safety and prevent devaluation of a plane.
Theory
The most paramount consideration in float construction [Figure 1] is the use of sturdy and lightweight material which is hydro-dynamically and aerodynamically designed to optimize performance. The material should also be as resistant to corrosion as possible. The most appropriate alloy for these requirements is steel. This alloy has the right properties to be used for the brackets.
Figure 1, Float Components.
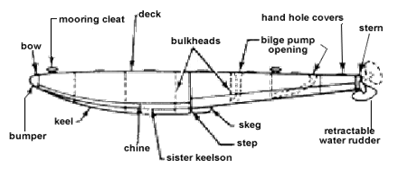
For instance, the mean shear strength of the steel alloy brackets is considerably greater than that obtained when other brackets are used. This is paramount particularly in need to withstand the plane’s load (Stickland, 2004). While an alternative such as aluminum is desirably lighter, it produces a lower mean shear bond strength values. The steel alloy consists of Iron (80–98%), carbon (0.2–2%), plus other metals such as chromium, manganese, and vanadium. Magnesium is highly corrosive and should be completely avoided in the alloy.
Brackets constructed of steel provides resilience from being struck or hit by objects in the water. Also, the brackets’ resistance can absorb the imbalanced forces generated by the by chine or the motions of the seaplane as it floats (Patent US7699262). These centrifugal force conditions are triggered by the planning/on-step condition of the plane that reduces the frictional effect of the floats on water.
Analysis
The manufacturing process is particularly crucial in preventing improper use of metals in floats given the harsh environment they are used in. The material should be stainless or cadmium coated. Thus, the electrical potential of the metal can be avoided consequently preventing excessive corrosion to the brackets (Iron and Steel Society, 2004). The manufacturer may also introduce contact of dissimilar metals. With different metals used in other parts of the plane; an electrochemical process is initiated where the steel becomes the cathode while the aluminum becomes the reactive anode. The electrolyte water conducts the resulting process. This can lead to galvanic corrosion which extremely devalues the plane. Further, the materials may not be insulated. This can be undertaken through conventional methods of insulation such as the use of Teflon tapes and coating steel with zinc chromate primer before using them with aluminum which makes the rest of the parts of the plane. Additional disadvantages linked to the present project consist of the reduction of the bow rise as well as stability drop at both high and lower speed step turns (Stickland, 2004). The body of the bracket is not contoured and modified to enhance its fluid, aerodynamic profile consistently entirely.
Conclusions and Recommendations
Detachability is restricted in the present design due to the high-speed impacts and the predisposition of the plane to damage during landing and flight. The recommended alternative can be the “fin” design that the retrofit is mounted to a current buoy or, in additional ideal applications, can be made into the initially planned buoy/float. This would serve to boost the simplicity of removability, for example, encourage using channel and space engagement between the primary bit and the surface of the buoy. Likewise, it stays away from the conceivable occurrence of a protest in the water hitting the section related with the moving buoy, which will bring about just the second bit to withdraw, in this manner counteracting harm to the associated float.
In a perfect application, either or both the parts of the sections are developed of a flexible and sturdy material, for example, including a polymer. The upside of which is the arrangement of a more prominent level of adaptability which allows the sections to flex or twist because of strolling or chine strengths of the middle of the road seriousness. They would likewise have the capacity to return to unique shape. In this way, accidental breakage of a section at the frangible area, for example, an aftereffect of over the top water driven powers.
It
is mulled over that additional variation of the design may incorporate more solid
metallic or other engineered material developments and, moreover, that the
sections might be further planned to be retractable either against or inside the
related buoys, while as yet holding their coveted element working and security
breakaway attributes.
References
Iron and Steel Society. (2000). Steel products manual: Carbon, high strength, low alloy, and alloy. Warrendale, PA: Iron and Steel Society.
United States. (2004). Seaplane, skiplane, and float/ski equipped helicopter operations handbook. Washington, D.C: U.S. G.P.O.
Patent US7699262 – Detachable hydrofoil trim tabs for use … (n.d.). Retrieved from http://www.google.com/patents/US7699262
Stickland, P. (2004). Planes. Columbus, Ohio: Waterbird Books